The harness in the car is an important part of the electrical system, mainly in the automotive electrical system to play the role of energy transmission and signal transmission. In the new energy vehicles, especially pure electric vehicles, in addition to 12V circuit system, there is a voltage of more than 300V is mainly used for power drive system circuit system, the system needs to use high-voltage wiring harness to connect the various units in the circuit. New energy vehicles in the low-voltage wire harness and fuel line wiring harness is not very different, the main difference is that high-voltage wire harness, high-voltage wire harness from the wiring harness material, production technology and equipment, etc. have changed greatly.
1, technology and standards
Whether it is hybrid cars, pure electric vehicles or fuel cell vehicles, are inseparable from high-voltage electrical systems. High voltage electrical system design to the parts, including high-voltage wiring harness (high voltage cable and high voltage interface) and power distribution (charging) electrical system. Pure electric vehicles and plug-in hybrids take over 300V high voltage and hundreds of amps of high current. High-voltage wire harness is a key component of high-voltage electrical systems, providing reliable operation and safety for electric vehicle operation.
Chart 1 Hybrid Powertrain High Voltage Wire Harness System Typical Structure
Chart 2 pure electric vehicle high voltage wiring harness system typical structure

High-voltage wire harness is the electric car inside the connector and cable in the whole car is very critical of the connection, the impact of high-voltage wire harnesses are mainly overheating or burning, and harsh environment should also have shielding performance of the harness, Dust and so on. Different from the traditional car 12V wiring harness, high voltage wiring harness also need to consider the magnetic compatibility with the vehicle electrical system. In actual use, electric vehicles are subject to electromagnetic interference is the traditional internal combustion engine car nearly a hundred times. The high-voltage wire harness of the electric vehicle is an efficient electromagnetic interference transmitting antenna and receiving antenna, which is the most important reason leading to the electromagnetic vehicle malfunction and radiation interference exceeding the regulations. High-voltage wire harness production of magnetic interference will affect the car signal line in the data transmission integrity and accuracy, serious will affect the vehicle control and security. Therefore, in the high-voltage wiring harness is often used outside the injection, shielding shielded wire, etc. to reduce the vehicle's magnetic interference. The EU also provides for the content of lead, mercury, cadmium, etc. contained in automotive wiring harnesses, which must be RoHS compliant.
China's voltage and high voltage wiring harness has not been a unified standard, previously implemented GB / T25085, GB / T25087 "road vehicles with 60-600V low voltage cable" born out of IS06722, rated voltage 60-600V single or multi-core cable Made the provisions and requirements, but for the use of new energy vehicles more than 600V high-voltage cable, there has been a standard missing and blank. As the rapid development of electric vehicle technology, high-power electric vehicles on the application of higher voltage is the operation of the operation, no standard, resulting in complex product structure, interchangeability is poor.
August 2016, the Ministry of Industry approved the release of the automotive industry standard QC / T 1037-2016 "road vehicles with high-voltage cable", and in September 1, 2016 formally implemented. This standard specifies the requirements, test methods, inspection rules, packaging and marking of high voltage cables for road vehicles with rated voltages AC 1000 V / DC 1500 V and below.
The rapid growth and maturity of the new energy automotive industry is the premise of the rapid introduction of high-voltage wire harness standards, the next few years is the peak of the growth of new energy vehicles, a list of public consultation is expected to gradually introduce and improve the standard, high-voltage wire harness industry will step and benign Rapid development of the track.
2, the market
On the market side, since the automotive wiring harness is a key component that affects the electrical performance of the vehicle, the world's major manufacturers and professional wire harness manufacturers usually maintain a long and close stable relationship. Global automotive wiring harness manufacturers a high degree of monopoly, the main four manufacturers occupy more than 75% of the market. Most of the Japanese car cable manufacturers were originally engaged in the production of wire and cable, a very good product technology heritage, at the same time, Sumitomo and other companies also master the upper reaches of the mining resources, cost control is better.
Figure 3 Global automotive wiring harness main production enterprises and market share
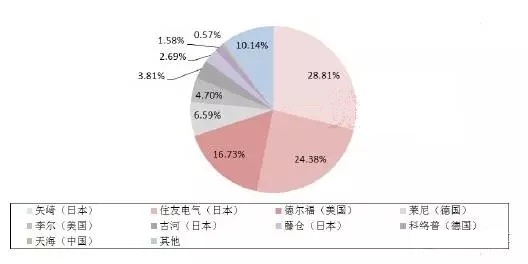
As China's automotive wiring harness industry started late, at present, most of the foreign or joint ventures, accounting for 42% of China's wire harness industry, followed by some of the larger private auto parts manufacturers, the share of 37%, while the state Harness business accounted for 21%. According to statistics, the current foreign investment in China's harness business has reached more than 100, the world's leading automotive wiring harness business almost all in China to establish a joint venture or wholly-owned enterprises.
Figure 4 Distribution of domestic wire harnesses
3, take advantage of the situation
Technology continues to progress: the development of high-voltage wire harness technology is also reflected in the wiring harness processing technology. The wiring harness voltage collection and temperature acquisition of the wiring harness on the crushing process requirements are high, high-voltage wire harness in the large diameter part of the terminal material due to restrictions, must use hydraulic equipment, can not use the traditional stamping process. In the processing of waterproof parts must be used when the new equipment, the smaller the amount of orders is not worth buying equipment, the wiring harness factory generally require the connector supplier has been crimping a good semi-finished wiring harness for secondary processing to ensure quality.
Lightweight trend: In order to reduce fuel consumption, the number of vehicles on the wiring harness to become the focus of the focus of the enterprise. The current use of automotive wiring harness materials mainly copper, so in addition to reducing the cross-sectional area in terms of weight loss, is the use of copper lighter than the aluminum material. The use of aluminum wire is also one of the future development trend, the current domestic wire harness enterprises are developing related technologies. In addition, the price of aluminum compared to copper cheap, once the aluminum wire can be applied in the wiring harness, not only can reduce the weight, but also effectively improve the price.
Overall, the past two years, some of our own enterprises in the development of high-voltage wire harness technology has made progress, but some of the core technology and equipment are still in the hands of foreign brands, technology and domestic prices of high prices. The lack of standards, the lack of industry regulation, leading to the quality of related products varies greatly. The core components of weak technology, localization rate is low, which is the new energy automotive auto industry is extremely rapid development of non-coordinated. However, some domestic enterprises have begun to walk in the forefront of technology and standards in the market layout has been rapidly carried out.