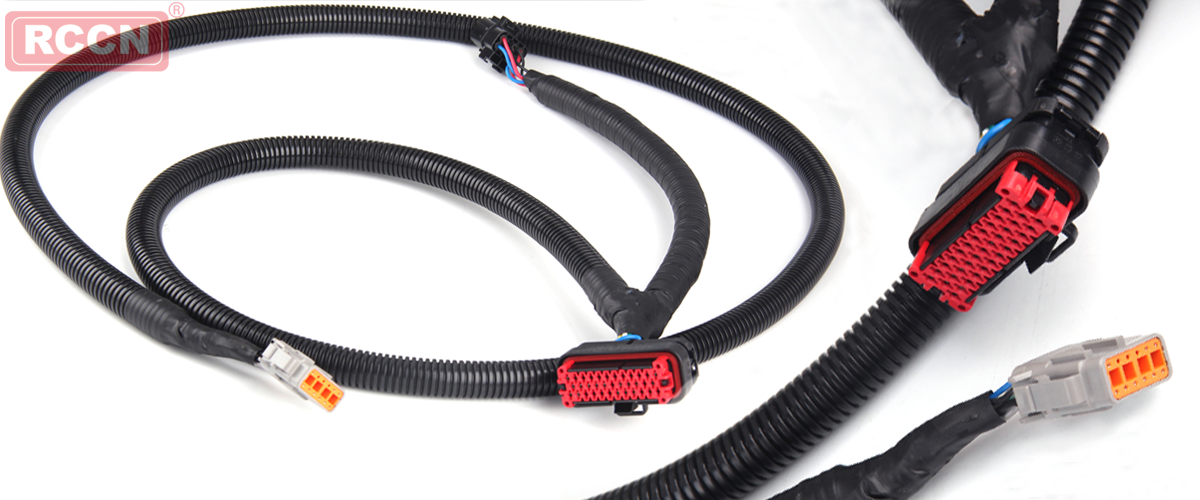
Repair of harness defects
1. Breakdown, hole, collapse pit and other repair methods: with a knife to repair defects, and cut into 45 ° angle of the slope shape of the same size of the plastic block, on the repair area, with a pliers or screwdriver fixed, and then use Hot air speed welding torch continuous welding, with copper compaction, compression, flatten. Welding plastic, pay attention to the torch hot air temperature should not be too high, so as not to repair plastic scorch. The defects of the wiring harness are tested by the spark machine, and the breakdown is not qualified.
2. broken glue, cracks, depression, holes and other repair methods: the knife in the plastic layer defect parts cut into 45 ° angle of the slope, to shape, color, thickness of the same plastic block or strip, with a pliers or a screwdriver fixed , With hot air speed welding gun connected, and then use copper pieces compaction, compression, flattened, the final wire by the spark machine test, not breakdown for qualified.
3. Ear, bulge, edge bag, wrinkle, etc. Repair method: the harness plastic defects with a knife flattened, with some of the same plastic strip in the hot air plastic welding gun filled with the role, and then with copper in the defect repair Flattening, pressing, compaction, by the spark machine test, not breakdown for qualified.
Large joint repair method
1. General large joints of the repair: the two sides of the broken glue with a knife in the plastic layer along the circumference cut into 45 ° angle of the slope, clean and clean, the same color and thickness, length and diameter consistent with the broken Plastic pipe, cut in the side of the tube along the axis of the opening angle of 45 ° for each other at the break in the broken, with fine copper wire equidistant tight, and then use the same plastic bar in the hot air welding torch welding, stick Then welded, and then copper plate compaction, compression, flattening. Spark machine test without breakdown for qualified.
2. In the production process of large joints repair: in the production process, due to other reasons in the temporary parking, jacket off, you can continuous joints. The method is to cut the plastic sheath into a 45 ° angle of the circular slope, retreated to the nose, into the core mouth 30mm long, and then run the glue, the glue ran well, the crew with each other, driving When the plastic layer with a hand to connect, and then plastic repair.
3. The cable jacket from the end of a long length of the quality defects on the other, while the other part of the broken jacket is good, cable length length, can also be used in the production process of large joints repair method. Just in the Pa to have quality defects in the end of the jacket, the extruder on the matching larger mold, according to the process of first squeeze the package to the end of the jacket to the big joints to gradually increase the speed of the traction to the interface gradually Thinning and wrapped in the cut into the original shape of the sheath, to be the next machine after the plastic repair.